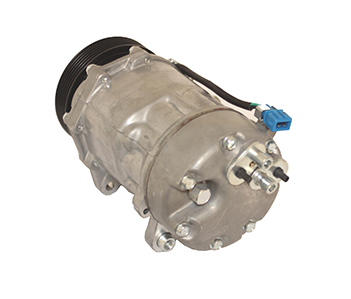
The Evolution of Double-end Piston Compressors in Industrial Applications
Explore the evolution of double-end piston compressors in industrial applications. Discover their design, advantages, and how they compare to other compressors. Stay updated on the latest technological advancements for a more efficient industrial future.
ZHONGCHENG
Double-end piston compressors, a vital component in various industrial applications, have undergone significant evolution over the years. This article delves into the historical development, technological advancements, and current trends in the use of double-end piston compressors across different industries. We will explore their mechanical design, efficiency improvements, durability, and how they compare to other types of compressors. Additionally, the article will discuss the future of double-end piston compressors, considering the latest trends in automation, energy efficiency, and material science.
Introduction
1.1 Overview of Piston Compressors
Piston compressors, also known as reciprocating compressors, have long been a staple in industrial settings. These machines are used to compress gas or air by reducing the volume of the gas, thus increasing its pressure. Double-end piston compressors, a specific type of reciprocating compressor, feature pistons that compress gas from both ends, enhancing efficiency and reducing operational costs.
1.2 Importance of Double-end Piston Compressors
The design of double-end piston compressors allows for greater output in a more compact form, making them ideal for applications where space and efficiency are critical. They are commonly used in industries such as oil and gas, chemical processing, manufacturing, and refrigeration, where reliable and continuous operation is essential.
Historical Development of Double-end Piston Compressors
2.1 Early Beginnings
The concept of piston-driven machines dates back to the 18th century, with early designs focusing on single-end piston compressors. These early models were simple and inefficient, often requiring significant maintenance. The need for more efficient compressors led to the development of double-end piston designs.
2.2 The Birth of Double-end Piston Compressors
The first double-end piston compressors were introduced in the early 20th century. These designs were initially used in large-scale industrial settings where the demand for high-pressure air and gas was growing. The dual-piston arrangement allowed for greater efficiency and higher compression ratios, which were critical for industrial applications.
2.3 Technological Milestones
Throughout the 20th century, advancements in materials, machining techniques, and design principles contributed to the evolution of double-end piston compressors. The introduction of new materials such as high-strength alloys and composites improved the durability and efficiency of these compressors. Innovations in sealing technologies and lubrication systems further enhanced their performance.
Design and Operation of Double-end Piston Compressors
3.1 Mechanical Design
Double-end piston compressors are characterized by their dual-piston arrangement, where two pistons are connected to a single crankshaft, operating in opposite directions. This design balances the forces within the compressor, reducing vibrations and wear on the components.
3.2 Working Principle
The basic working principle of a double-end piston compressor involves the intake, compression, and exhaust stages. As the crankshaft rotates, the pistons move in opposite directions within their cylinders. This movement creates a vacuum that draws in gas on one side while compressing gas on the other. The compressed gas is then discharged through an exhaust valve.
3.3 Advantages Over Single-end Piston Compressors
Compared to single-end piston compressors, double-end designs offer several advantages, including higher efficiency, reduced footprint, and balanced operation. The ability to compress gas from both ends of the cylinder allows for more continuous operation and greater overall output.
Industrial Applications of Double-end Piston Compressors
4.1 Oil and Gas Industry
In the oil and gas sector, double-end piston compressors are essential for compressing natural gas, refining processes, and in the operation of pipelines. Their ability to handle high pressures and maintain efficiency under continuous operation makes them ideal for these applications.
4.2 Chemical Processing
Chemical plants often require precise control over gas compression to maintain safe and efficient operations. Double-end piston compressors are used in various chemical processes, including the production of ammonia, methanol, and other industrial chemicals. Their reliability and ability to handle corrosive gases are particularly valued in this industry.
4.3 Manufacturing
In manufacturing, compressed air is used for powering pneumatic tools, controlling robotic systems, and other automated processes. Double-end piston compressors provide a stable and reliable source of compressed air, ensuring that manufacturing lines operate smoothly and efficiently.
4.4 Refrigeration and HVAC
Double-end piston compressors are also used in large-scale refrigeration and HVAC systems, where they are responsible for compressing refrigerants to maintain desired temperatures. Their high efficiency and ability to handle continuous operation make them well-suited for these demanding applications.
Technological Advancements in Double-end Piston Compressors
5.1 Material Innovations
The development of new materials has played a crucial role in the evolution of double-end piston compressors. High-strength alloys, ceramics, and composite materials have been introduced to improve the durability and performance of compressor components. These materials are particularly beneficial in applications involving high pressures and temperatures.
5.2 Efficiency Improvements
Modern double-end piston compressors are designed with a focus on energy efficiency. Variable speed drives, advanced sealing technologies, and optimized cylinder designs contribute to reduced energy consumption and lower operational costs. Additionally, advancements in lubrication systems have minimized friction losses, further enhancing efficiency.
5.3 Automation and Control Systems
The integration of automation and control systems has revolutionized the operation of double-end piston compressors. These systems allow for real-time monitoring of performance parameters, predictive maintenance, and automatic adjustments to optimize compressor operation. As a result, downtime is reduced, and the lifespan of the compressor is extended.
5.4 Environmental Considerations
Environmental concerns have driven the development of compressors that minimize emissions and reduce energy consumption. Double-end piston compressors are now being designed with features such as low-emission seals, energy recovery systems, and eco-friendly lubricants. These advancements contribute to the sustainability of industrial operations.
Comparative Analysis with Other Compressor Types
6.1 Single-end Piston Compressors
While single-end piston compressors are still widely used, they are generally less efficient than their double-end counterparts. The primary advantage of single-end compressors is their simplicity and lower initial cost, but they often require more maintenance and are less suitable for high-demand applications.
6.2 Rotary Compressors
Rotary compressors, including screw and vane types, offer advantages in terms of continuous operation and compact design. However, they may not achieve the same pressure levels as double-end piston compressors and can be less efficient in applications requiring variable output.
6.3 Centrifugal Compressors
Centrifugal compressors are often used in applications requiring very high flow rates and low to moderate pressures. They are typically more efficient than piston compressors in these scenarios but are not as versatile when it comes to handling a wide range of pressures and flow rates.
6.4 Diaphragm Compressors
Diaphragm compressors are specialized for applications requiring ultra-pure or hazardous gas compression. While they offer excellent sealing and low contamination risk, they are not as efficient or robust as double-end piston compressors in general industrial applications.
Conclusion
Double-end piston compressors have come a long way since their inception, evolving into highly efficient and reliable machines that play a critical role in various industrial applications. As technology continues to advance, these compressors will become even more efficient, durable, and integrated with modern industrial systems. The ongoing focus on energy efficiency, sustainability, and automation will drive further innovations, ensuring that double-end piston compressors remain a key component in the industrial landscape for years to come.
-
Boost HVAC Durability with Wobble Plate Type Compressors
2024-08-07
-
Advances in Variable-displacement Compressors: Balancing Performance and Efficiency
2024-07-31
-
Understanding Fix-Displacement Compressors in Modern HVAC
2024-07-25
-
Versatile Compressors for Emergency Vehicles
2024-07-19