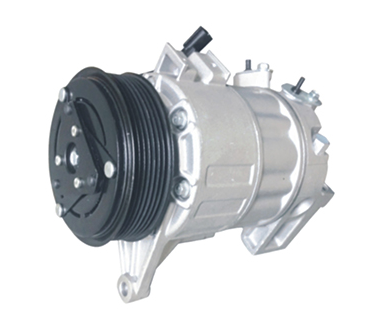
Enhance Industrial HVAC with Fixed-Displacement Compressors
Explore the role of fixed-displacement compressors in industrial HVAC systems. Learn about their design, applications, and how to optimize performance and energy efficiency.
ZHONGCHENG
Fixed-displacement compressors are integral to many industrial HVAC systems, offering a balance of reliability, efficiency, and simplicity. This article explores the role of fixed-displacement compressors in optimizing industrial HVAC systems, detailing their advantages, applications, and how they contribute to system performance and energy efficiency. We will examine key considerations for their selection, integration, and maintenance, alongside recent advancements that enhance their functionality.
Introduction
1.1 Overview of Fixed-displacement Compressors
Fixed-displacement compressors are a type of positive displacement compressor where the amount of gas compressed per cycle remains constant. They are commonly used in HVAC systems for their robustness and straightforward design. Unlike variable-displacement compressors, which adjust their displacement based on load requirements, fixed-displacement compressors operate at a constant capacity.
1.2 Importance in Industrial HVAC Systems
In industrial HVAC systems, fixed-displacement compressors are valued for their durability and cost-effectiveness. They are used in various applications, from cooling large facilities to providing climate control in manufacturing environments. Their ability to handle consistent loads makes them a suitable choice for many industrial processes.
Design and Operation of Fixed-displacement Compressors
2.1 Mechanical Design
Fixed-displacement compressors, such as reciprocating and screw types, have a simple mechanical design. They consist of a few moving parts, including pistons or screws, which create compression by reducing the volume of the gas.
• Reciprocating Compressors: Utilize pistons driven by a crankshaft to compress the gas in a cylinder. The piston’s movement creates a vacuum to draw in gas and compresses it to a higher pressure.
• Screw Compressors: Employ two interlocking screws (or rotors) that compress the gas as they rotate. This design is typically used for larger systems due to its high efficiency and reliability.
2.2 Working Principle
Fixed-displacement compressors operate by trapping a specific volume of gas and compressing it with each cycle. The process involves:
• Intake: Gas enters the compressor through an intake valve.
• Compression: The trapped gas is compressed by reducing its volume.
• Discharge: The high-pressure gas is expelled through a discharge valve.
2.3 Advantages and Limitations
Advantages:
• Simplicity: Fewer moving parts reduce the potential for mechanical failure.
• Reliability: Proven technology with a long history of successful operation.
• Cost-effectiveness: Generally lower initial cost compared to variable-displacement compressors.
Limitations:
• Energy Efficiency: Fixed-displacement compressors may be less efficient under varying load conditions.
• Operational Costs: May incur higher energy costs if the system operates under fluctuating demands.
Applications of Fixed-displacement Compressors in Industrial HVAC Systems
3.1 Large-Scale Cooling Systems
Fixed-displacement compressors are commonly used in large-scale cooling systems, such as those found in data centers, industrial facilities, and commercial buildings. Their ability to deliver consistent cooling performance makes them ideal for environments with stable cooling needs.
3.2 Manufacturing Facilities
In manufacturing, fixed-displacement compressors provide climate control for production environments. They ensure that temperature and humidity levels remain stable, which is crucial for processes that require precise conditions.
3.3 Refrigeration
Industrial refrigeration systems often use fixed-displacement compressors to maintain low temperatures in storage facilities, cold rooms, and other environments requiring controlled cooling.
3.4 HVAC for Special Applications
Special applications, such as process cooling and industrial ventilation, benefit from the reliability and consistency offered by fixed-displacement compressors. They are often used in conjunction with other cooling components to achieve the desired performance.
Optimizing HVAC Systems with Fixed-displacement Compressors
4.1 System Design Considerations
4.1.1 Load Analysis
A thorough analysis of the cooling load is essential to select the right fixed-displacement compressor. This involves calculating the maximum cooling requirements and ensuring that the compressor can handle these demands efficiently.
4.1.2 Integration with Other Components
Fixed-displacement compressors should be integrated with appropriate components such as heat exchangers, expansion valves, and controls to optimize system performance. Proper integration ensures that the compressor operates efficiently within the HVAC system.
4.2 Maintenance and Operational Efficiency
4.2.1 Routine Maintenance
Regular maintenance, including cleaning, inspection, and lubrication, is crucial for maintaining the performance of fixed-displacement compressors. This helps prevent breakdowns and ensures that the compressor operates at peak efficiency.
4.2.2 Performance Monitoring
Monitoring the performance of fixed-displacement compressors using sensors and control systems can help identify potential issues before they lead to system failures. This includes tracking parameters such as pressure, temperature, and energy consumption.
4.3 Energy Efficiency Improvements
4.3.1 Variable Frequency Drives
Installing variable frequency drives (VFDs) can improve the energy efficiency of fixed-displacement compressors by adjusting their speed based on the load requirements. Although VFDs are more commonly associated with variable-displacement compressors, they can also enhance the efficiency of fixed-displacement systems under certain conditions.
4.3.2 Advanced Controls
Modern controls and automation systems can optimize the operation of fixed-displacement compressors by adjusting their performance based on real-time data. This helps to reduce energy consumption and improve overall system efficiency.
4.3.3 Heat Recovery
Implementing heat recovery systems can capture and reuse waste heat from the compressor, improving overall energy efficiency and reducing operational costs.
Conclusion
Fixed-displacement compressors continue to play a vital role in optimizing industrial HVAC systems. Their reliability, cost-effectiveness, and straightforward design make them a popular choice for various applications. As technology advances, these compressors will evolve to offer even greater efficiency, performance, and integration with modern industrial systems. By focusing on design considerations, maintenance, and energy efficiency, industries can maximize the benefits of fixed-displacement compressors and achieve optimal HVAC system performance.
-
The Evolution of Double-end Piston Compressors in Industrial Applications
2024-08-15
-
Boost HVAC Durability with Wobble Plate Type Compressors
2024-08-07
-
Advances in Variable-displacement Compressors: Balancing Performance and Efficiency
2024-07-31
-
Understanding Fix-Displacement Compressors in Modern HVAC
2024-07-25