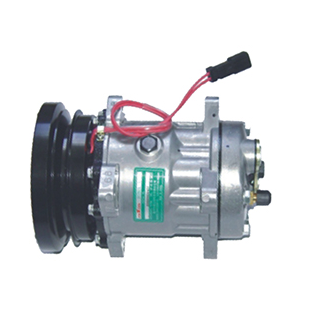
Variable-displacement Compressors: Adapting to Dynamic HVAC Demands in Automotive Applications
In today's automotive industry, the need for efficient and adaptable Heating, Ventilation, and Air Conditioning (HVAC) systems is paramount. Variable-displacement compressors have emerged as a key technology in this domain, providing enhanced performance, energy efficiency, and passenger comfort. Unlike fixed-displacement compressors, variable-displacement compressors can adjust their output based on the specific cooling demand, making them ideal for modern vehicles that require dynamic HVAC capabilities.
ZHONGCHENG
Overview of Variable-displacement Compressors
1.1 What are Variable-displacement Compressors?
Variable-displacement compressors are designed to modulate their capacity to match the cooling load in real-time. By adjusting the amount of refrigerant they compress with each cycle, these compressors can deliver just the right amount of cooling needed, leading to significant energy savings and improved system performance.
1.2 Types of Variable-displacement Compressors Used in Automotive HVAC
In automotive applications, several types of variable-displacement compressors are commonly used:
• Swash Plate Compressors: These compressors utilize a swash plate mechanism to change the angle of the pistons, allowing for variable displacement.
• Wobble Plate Compressors: Similar to swash plate designs, wobble plate compressors adjust their displacement by tilting the piston assembly, providing a compact solution.
• Scroll Compressors: Some scroll compressors are designed to operate in a variable-displacement mode, offering high efficiency and low noise levels.
1.3 How Variable-displacement Compressors Work
Variable-displacement compressors operate by changing their displacement based on the demand for cooling. The control system uses inputs from various sensors, such as cabin temperature and refrigerant pressure, to determine the required output. The compressor then adjusts its capacity accordingly, either by varying the angle of the swash plate or wobble plate, or by using electronic controls in scroll compressors.
Benefits of Variable-displacement Compressors in Automotive HVAC Systems
2.1 Energy Efficiency
One of the most significant advantages of variable-displacement compressors is their ability to enhance energy efficiency. By modulating their output to match cooling demand, these compressors can reduce energy consumption significantly.
• Reduced Load on the Engine: In internal combustion engine vehicles, variable-displacement compressors reduce the load on the engine by operating only as needed, which can improve fuel efficiency.
• Electric Vehicle Performance: In electric vehicles (EVs), efficient HVAC operation is crucial for maximizing battery range. Variable-displacement compressors help achieve this by minimizing energy use.
2.2 Improved Passenger Comfort
Variable-displacement compressors enhance passenger comfort by providing a more consistent and controlled cabin climate. The ability to adjust output in real-time leads to:
• Rapid Temperature Control: Variable-displacement compressors can quickly respond to changes in temperature settings, ensuring a comfortable cabin environment.
• Reduced Temperature Fluctuations: By continuously adjusting to the precise cooling demand, these compressors minimize temperature swings, enhancing passenger comfort.
2.3 System Integration and Flexibility
The adaptability of variable-displacement compressors allows for better integration with other vehicle systems, including:
• Thermal Management Systems: These compressors can work in conjunction with advanced thermal management systems to efficiently cool components like the battery in hybrid and electric vehicles.
• Adaptive Control Strategies: Variable-displacement compressors can integrate with smart control systems that optimize HVAC operation based on driving conditions and passenger needs.
Challenges and Considerations
3.1 Complexity and Cost
While variable-displacement compressors offer numerous benefits, they also come with increased complexity and cost. The advanced technology and control systems required for these compressors can make them more expensive to produce and maintain.
• Higher Manufacturing Costs: The complexity of variable-displacement designs leads to higher production costs compared to fixed-displacement compressors.
• Maintenance and Repair: The sophisticated control systems may require specialized knowledge for maintenance and repair, potentially increasing service costs for vehicle owners.
3.2 Control System Dependence
The performance of variable-displacement compressors relies heavily on the accuracy and responsiveness of the control systems. Any delays or inaccuracies in sensor data can affect the compressor's ability to adjust to changing demands.
• Sensor Reliability: The effectiveness of the compressor is contingent on the reliability of sensors that monitor cabin temperature and refrigerant pressure.
• Software Challenges: The software algorithms that govern compressor operation must be continually updated to adapt to new vehicle technologies and driving conditions.
3.3 Environmental Impact
As the automotive industry moves toward more sustainable practices, the refrigerants used in variable-displacement compressors must be considered. Many traditional refrigerants have high global warming potential (GWP), prompting the need for more environmentally friendly alternatives.
• Transition to Low-GWP Refrigerants: The industry is increasingly focusing on using low-GWP refrigerants, which can affect compressor design and efficiency.
• Regulatory Compliance: Manufacturers must stay ahead of regulatory changes regarding refrigerant usage, which can impact the design and operation of HVAC systems.
Optimizing Variable-displacement Compressors in Automotive HVAC Systems
4.1 Advanced Control Algorithms
To fully realize the potential of variable-displacement compressors, manufacturers are investing in advanced control algorithms that enable more precise and responsive operation.
• Predictive Algorithms: By utilizing predictive algorithms that consider factors such as weather conditions and driving behavior, the system can optimize compressor performance.
• Adaptive Control Systems: Implementing adaptive control systems can improve the compressor's ability to respond to real-time changes in cooling demand.
4.2 Integration with Hybrid and Electric Vehicle Systems
As hybrid and electric vehicles become more prevalent, optimizing variable-displacement compressors for these systems is essential.
• Battery Thermal Management: In EVs, variable-displacement compressors can be integrated with battery thermal management systems to ensure optimal battery performance and longevity.
• Efficient Heat Pump Operation: For vehicles using heat pump technology, variable-displacement compressors can facilitate efficient heating and cooling, enhancing overall system efficiency.
4.3 Use of Advanced Materials
Utilizing advanced materials in the construction of variable-displacement compressors can improve their efficiency, durability, and performance.
• Lightweight Materials: The use of lightweight composites and metals can reduce the overall weight of the compressor, contributing to better fuel economy in internal combustion engine vehicles and extending range in EVs.
• Enhanced Durability: Advanced materials can also increase the durability of compressor components, reducing wear and tear over time.
Innovations in Variable-displacement Compressor Technology
5.1 Electrification of Compressors
The trend toward electrification in the automotive industry is significantly impacting the design and functionality of variable-displacement compressors.
• Electric Variable-displacement Compressors: Electric compressors eliminate the mechanical link to the engine, allowing for independent operation and improved efficiency. This is particularly advantageous in hybrid and electric vehicles where optimizing energy use is critical.
• Integration with Smart Grids: Electrically driven variable-displacement compressors can be integrated with smart grids to manage energy consumption based on real-time energy pricing and availability.
5.2 Development of Smart HVAC Systems
The emergence of smart technologies in automotive HVAC systems is transforming how variable-displacement compressors operate.
• IoT Connectivity: Variable-displacement compressors equipped with Internet of Things (IoT) technology can communicate with other vehicle systems, allowing for real-time monitoring and adjustments to optimize performance.
• User-Centric Design: Smart HVAC systems can adapt to individual passenger preferences and driving conditions, providing a more personalized experience.
Conclusion
Variable-displacement compressors represent a significant advancement in automotive HVAC technology, offering a multitude of benefits including improved energy efficiency, enhanced passenger comfort, and better system integration. As the automotive industry continues to evolve toward electrification and sustainability, these compressors will play a crucial role in meeting the dynamic demands of modern vehicles.
Through continued innovation, advanced control strategies, and a focus on sustainability, variable-displacement compressors are well-positioned to adapt to the ever-changing landscape of automotive HVAC systems, ensuring they remain a vital component in the quest for efficiency and comfort in the vehicles of the future.
-
Celebrating the successful signing of Suzhou Zhongcheng-Dongfeng Nissan GK!
2024-09-13
-
Optimizing Industrial HVAC Systems with Fixed-displacement Compressors for Automotive Applications
2024-09-07
-
Scroll Type Electric Compressors: Key to High-efficiency Automotive HVAC Solutions
2024-08-28
-
Enhance Industrial HVAC with Fixed-Displacement Compressors
2024-08-23